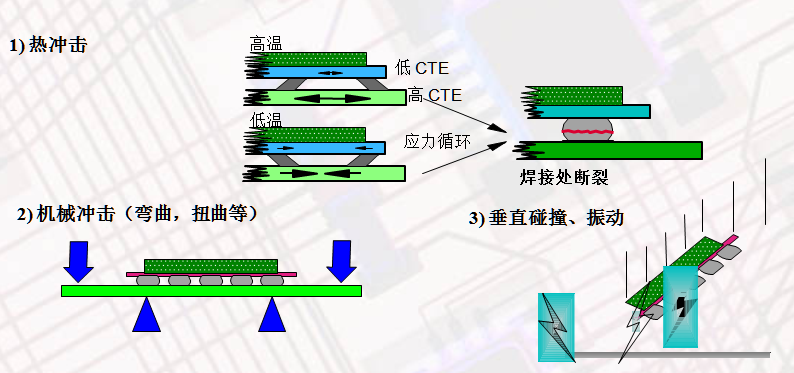
UNDERFILL底部填充胶之测试技术篇
我这里所说的底部填充胶之测试技术主要是站在客户角度的,至于UNDERFILL研发过程中考虑的因素会更多一些,但与客户的实际评估又有着许多不同的地方,虽然某些指标和客户的测试技术是相关的,但实际中往往是综合因素的影响,所以要了解客户的核心需求才能对应提供合适的产品。另外在UNDERFILL的理论研究中(论文什么的)就考虑考虑得更细了,其中还用了很多数学、物理及化学的模型及函数来分析(中间还还涉及到表面张力、接触角,回归分析…),这个就更不在我们的讨论之列了。
一、流动性:
流动性或者说填充速度往往是客户非常关注的一个指标,尤其是作为实际使用的SMT厂家,而实际对于可靠性要求非常高的一些行业,这个倒是其次的。就目前SMT行业的普遍要求,一般在1~30分钟理论上都是可接受的(当然手机行业一般是在2-10分钟以内,有些甚至要求以秒计,这个也需要结合芯片的大小)。
测试方法:最简单的方法当然是直接在芯片上点胶进行测试,而且评估不同胶水的流动性时最好是同时进行平行测试(最好样板数要5-10个以上)。在研发段对流动性的测试就是用两块玻璃片间胶水的流动速度来判断研发方向的。影响流动性的因素有很多,在平行的测试条件下,下面有些可以检讨的因素:
主要因素:
1)粘度:毋庸置疑粘度肯定是影响流动速度最关键的因素之一,目前像粘度在几百cps的胶水基本上都是可以不需要预热点胶的,填充速度基本上都是一两分钟以内的;而像粘度稍大一些的达到几千cps的胶差别就比较大了(从几分钟到十几分钟不等);
2)预热温度:这也是一个非常关键的影响因素,尤其是对一些粘度在一千以上的胶水,一般在预热(预热温度就需要结合各家的产品的特性,一般可以胶水的粘温曲线做参考,当并非一一直接对应的关系)的情况下,粘度为几千的胶水能降到几百,流动性会显著增大,但要注意预热温度过高过低都可能会导致流动性变差;
3)基板的差别(芯片的尺寸及锡球的分布、锡球球径及数量、锡球间距、助焊剂残留、干燥程度等),这个对填充速度也是有一定影响的,在某些情况下影响也是非常明显的。当然这些差别对另一个底填胶的指标影响更大,后面会细说。当然如果是几种胶水平行测试,这个因素的影响是一致的。
次要因素:
1)施胶量(点胶方式);
2)基板角度(有些厂家会将点胶后的基板倾斜一定角度加快流动性);
3)环境温度(不预热的情况下)
说明:以上的一些因素的主次也都是相对而言的,如果客户能接受预热的方式的话,同时客户对流动性的要求不会精确到秒的话,那么上述因素的影响都会变小了。不预热的情况下要求快速填充的话,除了把胶的常温粘度做小外貌似没有更好的办法(像乐泰的UF38XX系列的底填也是被这个要求逼出来)。另外同样是预热的条件下,流动速度就和胶水体系自身的设计思路有很大的关系了。同样一款2000cps左右粘度的胶水,预热的情况下流动速度也可以差几倍时间的。最后对于预热这个环节每家的说法都不一样,很多客户不愿意预热其实也是为了点胶操作的便利性,然而站在理论分析的角度,基板预热可以起到烘烤芯片的作用,而且也可以减少填充时产生空洞(气泡)的概率,当然加快填充速度也是必然的。在我的印象中,在苹果手机出现之前,乐泰是没有低于1000cps的底填胶水型号的,虽然那个时候之前Zymet公司就一直在推出粘度300左右的底填胶水(这个化学体系的胶水在某些条件下会有着致命的缺点,换一个研发工程师的说法是用这个体系来做UNDERFILL其实是投机取巧的方法,后面在底填胶的化学体系中我会再细说)。估计也是基于这个原因,乐泰之前一直都是推以3513为代表型号的底填胶水,而这个型号在使用中也是建议客户预热使用的,包括元化学的WE-1007等都是通过预热来改善流动性的;
二、固化温度和时间(固化度)
这个指标其实在研发端是比较容易判断的,用DSC曲线就很容易判断出来,当然由于DSC在测试时胶量是以mg来测试,所以一般建议给客户的固化温度是在DSC的理论时间上乘以4倍的(韩国元化学的建议)。
然而在客户端如果判断,其实简单的方法就是按胶商TDS上建议的固化温度和时间还是比较保险的。另外有些客户经常会问如果不完全按TDS建议会如何,简单的推断的方法同等温度下时间加长或者同等时间下温度升高,理论上都是会完全固化的,但反向推断的话最好找供应商确认下。因为每种胶特性不一样,低于某个温度时间即使加几倍时间也未必能固化,同理也不是温度越高时间就会越短,就目前接触到的底填胶水的固化温度没有建议高过150度的(SONY曾经有款手机,使用SUNSTAR的胶水,在150度快速固化时后期测试时会有些缺陷,同样改用130度加长时间固化后就没有这个问题了)。太高温固化和太快速固化对胶水的后期一些性能还是有着蛮大的影响的(有些体系的胶水会影响更明显)。这个道理喝过汤的朋友应该能理解一些,好汤可都是慢慢熬出来的,呵呵!
另外对于固化程度的判断,这个做为使用者的客户可能不大好判断,因为目测的完全固化时间和理论上的完全固化还是有差别的,客户一般容易从固化后的硬度,颜色等判断,但这个些指标可能在胶水只固化了80%以上时已经没法分辨出来了,如果能增加一些粘接力等测试辅助可能会更准确些,当然更精确的方法还是要用会DSC等一些热力学测试的设备和方法了。而在实际应用中,胶水达到90%或95%以上的固化已经算是完全固化了,具体要达到百分之九十几这个就要看后期可靠性的要求了。
未完全固化的胶水是很难真正全面发挥应有作用的,尤其是后期测试要求很严格的时候。所以建议客户最好使用相对保险的固化条件,如果设置在临界值的话,固化温度或固化时间少有偏差就可能导致固化不完全。
三、填充效果
这个指标其实也是客户比较关注的,但是对填充效果的判断需要进行切片实验,这个在研发端其实很难模拟的,而在客户这边一般也只有相对比较大型的客户才有这样的测试手段和方法,当然也可以送赛宝或者CTI华测等公司进行检测。
测试方法和设备(以赛宝为例):
检测项目:金相切片分析;
检测方法:IPC-TM-650 2.1.1 Microsectioning, Manual Method;
检测仪器:立体显微镜 金相研磨机 金相显微镜
几点说明如下:
1) 这个方法其实并不是针对底填胶的设立的,在电子行业原本是用于PCB信赖性实验,当然“微切片(Microsection)技术范围很广,PCB(Printed Circuit Board)只是其中之一。对多层板品质监控与工程改善,倒是一种花费不多却收获颇大的传统工艺。微切片制作是一件复杂的事情,说来话长一言难尽。要想做一个好切片,要考虑到“人机物法环(4M1E)”诸多因素,关键的地方要把握好。”,此段摘自《PCB微切片手工制作》;后期很多公司内部建立的方法也是参考此方法自行设立的。
2) 另外作为填胶后BGA的切片有横切和纵切之分,而横切也分为从BGA芯片部分打磨还从PCB板部分打磨两种方法。一般而言是用横切的结果来判断填充的整体效果,而用纵切的方法来判断胶水与锡球的填充性(助焊剂兼容性);
3) 前面提到,打磨(微切片)这个过程是比较复杂的,因为打磨过程可能造成对样品或胶层的意外破坏,这样就给后期判断增加了难度,所以当出现一个特别异常的切片结果的时候我们也需要从实验过程中找一些原因;
4) 对于最终的填充效果,这个没有绝对的标准,一般都是需要进行平行对并且还要结合后期的一些测试的。
而在客户现场对填充效果的简单判断,当然就是目测点胶时BGA点胶边的对边都要有胶水,固化后也是需要四条边的胶要完全固化,且没有任何肉眼可见的气泡或空洞。理想的状态是四边的胶都均匀爬到芯片边缘的一半处(芯片上不得有胶),这个其实和点胶工艺比较相关。另外整体的填充效果和前面讲到的填充速度其实一有一定关系的,尤其是前面谈到的流动性的主要因素3,当然和胶水也有较大的关系。从目前我接触到的各大厂家的测试报告中,没有哪家是可以百分百完全填充的,这里面另一个重要的影响的因素就是锡膏和助焊剂与胶水的兼容性,极端的情况下可能会导致胶水不固化而达不到真正的保护作用。
四、返修效果
关于返修效果,这个是一个相对更难量化的标准,就目前市面上常见的胶水,其实基本都是属于可返修型的,如果要从返修效果来分估计只能分成易返修、可返修和难返修三种,而将胶水的返修程度归到哪一类其实与返修的人、返修设备及返修方法、返修的时间等有着很大关系。
目前在返修环节碰到的一个最常见的问题就是焊盘的损伤,或者称之为掉焊盘,一般容易掉的都是空焊盘(没有了铜箔的互联,与基板的附着力当然要差一些),所以后来在一些公司的返修判断标准中将掉空焊盘也作为可退让接受的。
另外关于返修最近有些客户又提出一些新的问题和疑问,一种是固化后当天做返修测试,一种是固化后放置几天后再做返修测试,还有就是几个月后做返修测试(这个一般估计是产品回厂返修),这三种情况下同一款胶的返修成功率也会差异比较大,一般的规律当然是时间越长返修率越低。当然也有同一款胶三者的差别不是特别明显的情况,究前者的原因的话估计又回到固化程度的问题了(如果胶没有完全固化的话当时测试返修当然会容易些,当放置的时间长了后固化难度自然就加大了)。所以判断返修效果时最好要保证胶水能得到完全的固化。
另外还有个残胶清除的问题,这个其实没什么特效的方法,当然一些有机溶剂如丙酮等或清洗剂能辅助除胶,但是也是需要利用加热的方法及物理外力将残胶最终清除的。
上面讲了四个底填胶相关的测试要求,但貌似和底填胶本来起的作用并不直接相关,回头看看底填胶的描述中的核心作用:“能有效降低由于硅芯片与基板之间的总体温度膨胀特性不匹配或外力造成的冲击”。其中一个是外力的影响,另一个是温度(热冲击)的影响。下面的几个测试要求就是与这个相关的。
五、跌落试验
跌落试验是能比较明显显现处使用底填胶和未使用底填胶之间的差别的,据之前汉高公司发布的一些资料来看,正确的使用了底填胶水后,耐跌落的次数会比之前成倍的提高。但是跌落试验其实影响的因素也很多,另外与实验的方法和标准也有很大的关系,就之前接触到的一些方法和大家分享:
1) 跌落样品的制备:这里一般有几种情况,第一种是制作一批实验板(板上就只有BGA元件),第二种是直接将手机的主板作为测试样品(这里也分已焊接其余元件和未焊接其余元件),第三种就是直接将产品成品(手机、相机等)作为测试。这个取决于每家公司自己设置的标准。往往第一种在某些测试条件下可以达到几千次的跌落,而后面两种一般设置的标准都不超过三位数,因为后面两种情况跌落了若干次以后,主板本身或者外壳等早已跌坏了。
2) 跌落方法的设置,一般在以上第一种样品的情况下都会做负重跌落,及在样品上有额外加上一定的重量,整机跌落一般不加负重,主板跌落的话就要看测试方的要求了。而作为承跌的地面也有分不同,有些是橡胶地面、有些是普通的水泥或瓷砖地面、更有甚者是金属地面。而跌落高度一般是1-1.5米不等。跌落方式以抛物线方式或垂直跌落等方式为主。
3) 跌落的标准,这个就看每家公司自己的要求了。有一种标准是不限次数跌落,跌坏为止;一种是设定特定的跌落次数,能达到及视为通过跌落测试。就之前参与HW公司的评估,他们的标准就是2000次以上合格,3000次以上优秀,超过3000次就不再往下测试了。而之前和韩国元化学沟通得知的三星一般也是以1000次以上作为衡量标准的,但具体测试方法就不得而知了。
关于跌落额外说几句,如果测试方法不科学的话有时可能没法辨识使用底填胶的效果,我记得当时在MOTO还是SUNNY哪家公司,当时打胶不打胶最后测试出来的跌落次数是一样的,甚至打了胶跌落次数还少一些,所有有些厂商甚至一段时间还放弃了使用底填胶。
另外还有一个与跌落测试类似的测试,好像是叫阻尼测试还是什么的,有点类似滚筒测试什么的。而据元化学的介绍,他们后期推出替代WE-1007的型号WE-3008就是由于这个要求而改善的,前者好像只能达到几千次,而后者可以达到上万次。这个结论在HW公司的UNDERFILL评测中也得到了验证(虽然当时这项并不是他们的测评的标准)。其实从硬度就能明显看出差别了。前者的硬度约为邵D 级别,而后者却只有邵A的级别。不过由于主板的轻薄化,对胶的韧性提出要求应该也是趋势之一。
六、表面绝缘电阻
这项指标如果简单的测一次的话是比较容易的,而且一般就环氧体系而言这个值一般都是符合电气方面的要求的,客户比较比较关注的是经过老化后的此参数的维持情况,因为有些材料经过恒温恒湿或相关老化后此参数会发生比较大的变化,导致不符合电气方面的要求。我手上有一份赛宝针对底填胶SIR的相关测试,摘录相关方法如下:
检测项目:表面绝缘电阻
技术要求:参考IPC J-STD-004B Requirements for Soldering Fluxes(大于10^8欧姆以上)
检测方法:参考IPC-TM-650 2.6.3.7 Surface Insulation Resistance(双85下168小时)
检测仪器: 高低温交变潮热试验箱;SIR在线测试系统;立体显微镜;高温箱
几点说明如下:
1) IPC J-STD-004B这个技术要求其实是针对阻焊剂的,因为底填胶这个产品并没有自身的相关标准,很多都是参考IPC里面关于其它材料的标准建立的,如之前的金相切片实验也是如此;
2)对于环氧体系的胶水(非为导电设计)而言,一般情况下其表面绝缘一般都是在10的12~16次方以上,即使经过了相关环境试验的考验,最多就下降一到两个数量级就稳定了,所以通过以上测试不是什么太大的问题
七、温度循环(冷热冲击)
关于此项测试,英文一般称之为Temperature Cycling(Thermal Cycling),简称为TC测试。而在实际的测试中有两种情况,一种称之为温度(冷热)循环,而另一种称之为冷热(高低温)冲击。这两种其实对测试样品要求的严格程度是相差比较大的,如果设置的高温和低温完全一样,循环的次数也一样,那么能通过冷热冲击的样品一定能通过冷热循环,反之却就未必了。两者最大的区别就是升降温速率不同,简单的区分:速率为小于1-5摄氏度/分钟的称之为循环;而速率为大于20-30度/分钟的称之为冲击。关于这个可是花了几万块换来的经验和教训。TC测试除了这个升降温速率比较关键外,还有两个参数也需要关注,一个就是温度循环的区间(高温减去低温的差值),另一个就是在高低温的停留时间。当然这三个条件里面第二个温循区间其实最关键的。按日本SUNSTAR传达的SONY那边的TC测试要求,作为消费电子一般而言温循区间不超过100度,而作为工业或汽车电子方面要求温循区间是130度以上甚至更高。之前参加一家国内手机厂商此项测试时,咨询韩国元化学在三星的TC测试结果时告知可达到1000次以上,而实际在国内这边的测试是没有达到的,估计也是相关测试条件相差比较大。国内这边做的是温循区间为180度(-55到125度)的冲击(温度转换5分钟内)试验,包括后面将此测试要求告知日本SUNSTAR日本方,他们说普通的底填胶估计能通过的难度较大,推荐我们使用不可返修高可靠性的型号(用于汽车电子和工控设备的)尝试,不过这种是高粘度且不可返修的,估计手机厂商是不会考虑的。
关于温度循环测试除了制定的测试条件外,前面提到的两个指标其实也是对测试结果有蛮大的影响的。一个是前面提到的填充效果的确认,如果填充效果不理想,太多的气泡空洞或者由于锡膏助焊剂产生的兼容性问题的话,后期参与TC测试的效果肯定也是会打折扣的,有很多公司把切片实验放在前面,如果切片效果显示填充不理想的话,往往不会再继续往下进行TC测试的,毕竟成本和时间都要花费不少。另个影响因素就是固化度,理论上当然是固化越完全的话参与TC测试的效果是有正向作用的(固化越完全理论上交联密度越大),否则可能在TC测试中发生二次固化或者其他一些不可预期的反应,对测试效果影响也会很大的。
另外对于TC实验影响比较大的两个胶粘剂自身的参数是玻璃转化温度(Tg点)和底填胶固化后的CTE(热膨胀系数)。理论上Tg点越高,CTE越低(Tg前后的CTE值都较低且两者差值较小)通过TC测试的效果会更好。但追求这两个参数的时候又需要注意兼顾前面提到的返修性及流动性的要求,这应该是底填胶的一个难点。另外模量与Tg和CTE之间的匹配关系也是很重要,当具体需要怎样设计可能又需要上升到理论研究的层面了。
八、 其它测试(指标)
这里提到的测试或指标其实是在实际应用中客户有提到,但并不与胶水的核心作用直接相关的,而是基于客户的使用习惯、产线配置等而提出来的,或者说这些要求有时候是有点吹毛求疵的。
1)颜色:这个其实也是一个使用习惯问题,按目前市场的需求以黑色和浅色(淡黄或半透明)为主。当初在国内推广韩国元化学的WE-1007时是淡黄色的,后来为了迎合中国市场的需求推出了黑色的WE-1007BLA产品,同样后期推出的WE-3008也分了浅色和黑色两个版本。而实际在韩国三星使用的一直是浅色系的,包括最新推出的WE-3008S1已经快接近透明了。而除了这两种颜色外,市面上也有一些透明、深黄色、乳白色、棕色甚至蓝色的底填胶产品,这个就要看客户自己的选择了。有些客户觉得深色便于观察,有些觉得浅色觉得美观。对了市面上还有一家的底填胶水在里面加了荧光剂,在观察填充效果尤其是在POP填充时观察填充进度时会比较方便,技术上应该不是什么太复杂的事情;
2)硬度:这个指标往往山寨厂比较关注,很多时候他们只需要胶水能流过去,固化后用指甲掐掐硬度,凭感觉判断一下(在他们眼中貌似越硬越好)。这个其实和胶水本身的体系有较大的关系,像韩国元化学的WE-1007完全固化后硬度大概在Shore D 80以上(基本手指掐不动),而WE-3008完全固化后只有Shore A 60多(可以掐出手指印),所以有时候习惯了高硬度的客户初次使用时总担心没固化完全(在BBG的测试中,他们之前使用的是乐泰3517,固化后硬度为Shore D 88,而WE-3008的只有Shore A 64,固化后偏软,总让人觉得不放心,后来韩国提供了几个温度下的DSC曲线才消除了他们的疑虑。)
3)气泡和空洞:这个其实是用来评估填充效果的,前面在写填充效果时有提到相关影响因素的。就目前市场面常见粘度的底填胶,胶体内藏气泡的可能性比较小,据我们之前的经验,像3513或WE-1007之类粘度为3500cps左右的胶水,从大支分装到小支后,也只需要通过自然静置的方式也是可以将气泡排出的(当然用脱泡机处理一下当然是有备无患的),粘度更低当然就更容易自然排泡了。而在客户端测试时产生的一些气泡更多是填充的方式和施胶设备及基材的清洁度导致的。曾经有个客户居然用四边点胶的方式,这样必然会将空气包在芯片底部,填充效果肯定是不行,加之固化时里面包裹的空气膨胀,严重的时候甚至会直接在固化时的胶体上冲出气孔来。真正在切片阶段发现的气泡或空洞才是关注的重点,我博客里面有一篇namics公司写的关于气泡和空洞的成因及影响,比较详尽,大家可以搜索出来看看;
4)气味:作为化学品,其实多多少少都有一些气味的,这就要看使用者的习惯了,当然有时候也只是现场操作人员的一个托词。当然不同体系间的胶水的确气味上有一些差别,比较明显的像聚氨酯体系的底填胶水,其气味相对环氧体系就要大一些。另外在固化过程和返修过程中由于受热等因素,也会产生不同的气味,个人觉得主要是习惯就好了。本来一般在胶水的MSDS上,使用的过程中都建议戴防护用品的,只是很多公司嫌麻烦都没有专门去遵守罢了。但如果是溶剂型的胶水大量使用时,戴防护用品还是很有必要的。有些胶水里面使用了遮味剂,反而给使用者造成假象,放松了警惕;
5)耐温性:这也是客户经常问到的一个问题,关于胶粘剂的耐温性问题,我博客有篇文章有专门写到,大家可以去那里看看。作为底填胶,一般涉及到耐温性的需求其实是个别厂家的特殊要求。在SMT组装段,一般点底填胶固化是最后一个需要加热的步骤了。然而在有些厂里面可能会让已经填好胶固化后的主板再过一次回流炉或波峰焊(可能也是因为需要补贴BGA之外的一些元器件),这个时候对底填胶的耐温性就提出了一些考验,一般底填胶的Tg点不超过100度的,而去承受260度以上的高温(已经快达到返修的温度了),要求的确是很苛刻的。据国内一家手机厂商用二次回流的方法(回流焊260℃,7~8min)来测试底填胶的耐温性,测试结果基本上是全军覆没的。这里估计只能使用不可返修的底填才有可能实现了;
6)粘接强度:对于这项指标,其实一般也是不做要求的,因为底填胶本身不是做粘接作用的,而且即使填充到芯片底部,芯片与基板的牢固程度也主要是靠锡球焊接实现的,而并非由胶来实现。但是在实际测试中,有些客户也喜欢凭感觉的去判断胶水的粘接力,例如直接在PCB没有元件的地方点少量的胶固化后尝试用手去剥离,有时候也是能有个大概的感觉,就和前面用手掐感知胶水固化后的硬度一样。一般而言较硬的胶粘接力会大一些,而硬度较低的会小一些,像元化学的WE-3008和SUNSTAR的991等相对粘接力就会小不少。如果粘接力太大,会在另一个测试环节中有隐患,那就是返修,如果粘接力太大(尤其是在高温下的粘接力保持太大),就比较容易产生掉焊盘的问题;
7)阻抗:这个指标也只是在一个比较较真的客户那里碰到,关于阻抗的定义大家可以去百度百科看看(阻抗),当时的情况是我们提供的一款胶水在液态是有阻抗,而固化后没有,客户提出了质疑,我觉得我们的研发回答得还是比较在理的(产生阻抗的原因主要是该体系底填胶中某些组分在外加电场作用下极化现象引起的,未加热前,体系中某些组分因外加交变电场产生的偶极距较大,因此有一定阻抗,加热后,产生偶极距的组分发生了化学反应,反应后的产物偶极距非常小,因此阻抗很小甚至不能检测出),当时也说服了客户进行下一步的测试。不过迄今为止还没有第二个客户提出过类似的问题。
以上是对底填胶的相关测试和指标做了一个大概的分析,但在实际测试中,能将上面全部测试做完的基本上也是很大的厂商了(加上可靠性测试一般都要几周以上的时间了)。而一般的小厂商很多指标其实也只能参照性的做一下。另外国内的手机厂商对以上测试指标标准的设立也是在摸索中,有时候将某些指标要求设置过高到最后几乎所有的胶水都达不到要求,或者设立了两个相互矛盾的指标要求,最后也导致没有一款胶水能通过所有的测试。在与国内厂商的工程师交流时,他们也非常关注像三星索尼等公司评估胶水的标准,其实我们也没有现成的资料,其实适合自己的才是最有意义的标准。最后共享一份2007年和2008年在桑菲公司(他们现在好像也没怎么做手机了,所以资料共享出来应该对他们影响不大,报告中隐去了当时的工程师和相关技术人员的名字)的UNDERFILL胶水测试报告,个人觉得设置的测试条件和方法是比较简单实用的,对于首次评估底填胶的公司有一定的借鉴作用的。